Aluminum Casting Mastery: Strategies to Elevate Your Manufacturing Process
Aluminum Casting Mastery: Strategies to Elevate Your Manufacturing Process
Blog Article
Study the World of Aluminum Spreading: Comprehending the Various Methods
Aluminum casting is a basic procedure in the manufacturing industry, with various approaches utilized to produce specific and complex components. Understanding the different strategies made use of in light weight aluminum casting can provide valuable understandings right into the abilities and restrictions of each method. From the typical sand casting technique to the innovative die spreading process, each approach uses unique advantages relying on the needs of the project. Discovering these varied approaches can supply a comprehensive sight of the possibilities within the world of light weight aluminum spreading and just how each strategy adds to forming the modern manufacturing landscape.
Sand Casting Approach
Sand casting, a widely-used approach in aluminum casting processes, includes creating mold and mildews made from compacted sand for pouring molten steel. This method is cost-efficient and highly versatile, making it a preferred choice for numerous sectors. The process begins with the creation of a pattern, generally constructed from wood or metal, which is after that pressed into the sand to leave an impression. The sand combination, normally silica sand mixed with a binder like clay, is firmly packed around the pattern to create a mold tooth cavity. When the mold and mildew is ready, it is firmly placed in a flask and molten light weight aluminum is put right into the cavity.
After the metal has cooled down and strengthened, the sand mold is broken away to disclose the light weight aluminum spreading. Sand casting enables the production of intricate shapes and big components that might be pricey or challenging to create utilizing various other methods. It is also a lasting strategy as the sand can be recycled and used numerous times, minimizing waste in the casting process.
Irreversible Mold Method

One significant benefit of the Irreversible Mold And Mildew Strategy is the boosted dimensional precision it uses. The metal mold enables for tighter tolerances and finer information in the last light weight aluminum spreadings compared to sand casting methods. This precision makes it a recommended selection for applications where limited dimensional control is vital, such as in the vehicle and aerospace markets.
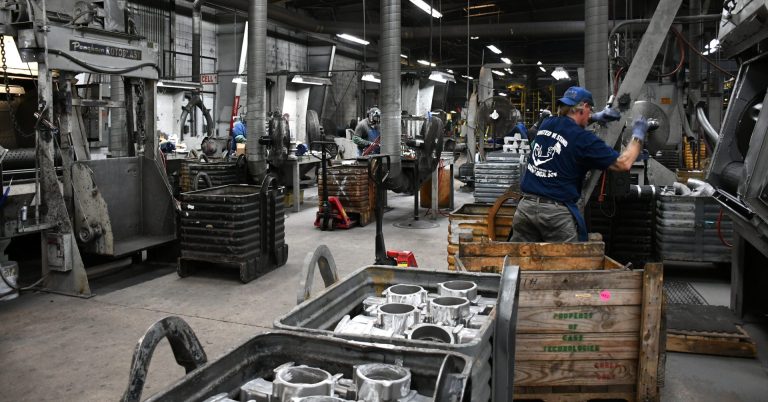
Die Casting Process
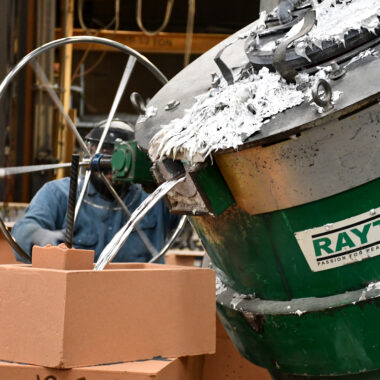
Investment Casting Approach
Using a precision spreading technique, Investment Casting Approach entails producing intricate light weight aluminum elements by pouring molten steel into a ceramic mold. This procedure, likewise known as lost-wax spreading, begins with the creation of a wax pattern of the wanted part (aluminum casting).
Financial investment casting is frequently used for producing parts in industries where tight resistances and detailed designs are needed, such as aerospace, vehicle, and clinical equipment. The flexibility and accuracy of the Financial investment Casting Strategy make it a valuable method in the globe of light weight aluminum spreading.
Lost Foam Casting Approach
Having actually explored the elaborate precision of Investment Casting Technique, the emphasis currently changes to the cutting-edge method of Lost Foam Casting in aluminum component manufacturing. Lost Foam Casting, also referred to as evaporative pattern casting, is a contemporary method where a foam pattern of the preferred component is created and after that covered with a refractory material. The layered foam pattern is after that hidden in sand, and molten aluminum is poured into the mold and mildew. As the steel fills the mold, the foam evaporates because of the warm, leaving a clean tooth cavity in the shape of the preferred part.
One of the main benefits of Lost Foam Spreading is its capability to produce complex forms with complex details, frequently in a single item without the need for additional machining. This approach is likewise known for its high dimensional precision and smooth surface finish. In Addition, Lost Foam Casting is an economical process as it lowers the requirement for cores and enables the manufacturing of lightweight parts. In spite of its advantages, Lost Foam Spreading requires mindful control of the casting procedure to stop defects and make certain quality parts.
Conclusion
To conclude, light weight aluminum spreading offers a variety of techniques such as sand spreading, permanent mold method, pass away casting, investment spreading, and shed foam spreading. Each method has its own benefits and applications, making light weight aluminum casting a versatile and commonly utilized procedure in various industries. Comprehending the distinctions in between these go to my blog approaches is important in picking one of the most ideal casting technique for particular manufacturing needs.
Sand spreading, a widely-used approach in aluminum spreading procedures, entails creating molds made of compacted sand for pouring molten metal. aluminum casting.The Permanent Mold Method, like sand casting, is one more common technique utilized in aluminum casting processes, providing distinct benefits in terms of mold and mildew reusability and dimensional accuracy. The metal mold enables for tighter tolerances and finer details in the last light weight aluminum spreadings contrasted to sand spreading techniques. The 2 primary types of die casting are cold chamber die casting and warm chamber pass away spreading, each appropriate for different types of aluminum alloys.In verdict, light weight aluminum spreading provides a variety of methods such as sand spreading, irreversible mold and mildew method, die casting, investment casting, and shed foam casting
Report this page